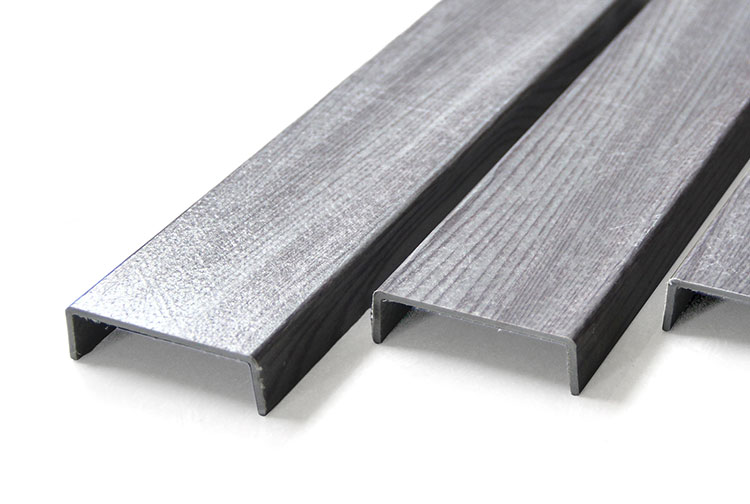
Fiber Mat in FRP Profiles
Introduction
Fiber Reinforced Polymer (FRP) profiles have become a critical component in industries such as construction, automotive, aerospace, and marine due to their lightweight, high strength, and corrosion resistance. Among the key reinforcements used in FRP manufacturing, fiber mats play an indispensable role. This article explores how fiber mats affect the performance of FRP profiles and why choosing the right mat can make a significant difference in structural integrity and durability.
What Is a Fiber Mat?
A fiber mat, commonly made from glass fibers, is a non-woven reinforcement material used in composite structures. It consists of chopped strands or continuous fibers bonded randomly or oriented in specific patterns. Fiber mats are typically used in conjunction with resin systems and form the core of many pultruded and molded FRP components.
Types of Fiber Mats
Type | Description | Typical Applications |
---|---|---|
Chopped Strand Mat (CSM) | Randomly oriented chopped fibers bonded with a resin-compatible binder | General FRP panels, pipes, boat hulls |
Continuous Filament Mat (CFM) | Continuous strands laid randomly to form a dense mat | High strength components, structural profiles |
Needle Mat | Fibers mechanically entangled without binders | Heat insulation, vibration dampening applications |
Fiber Mat in the Pultrusion Process
In the pultrusion process, dry fiber mats are pulled through a resin bath and into a heated die where the resin cures and forms a rigid profile. Fiber mats serve as the primary reinforcement in this process, providing volume, strength, and shape stability. Their orientation and quality directly affect the mechanical properties of the final FRP product.
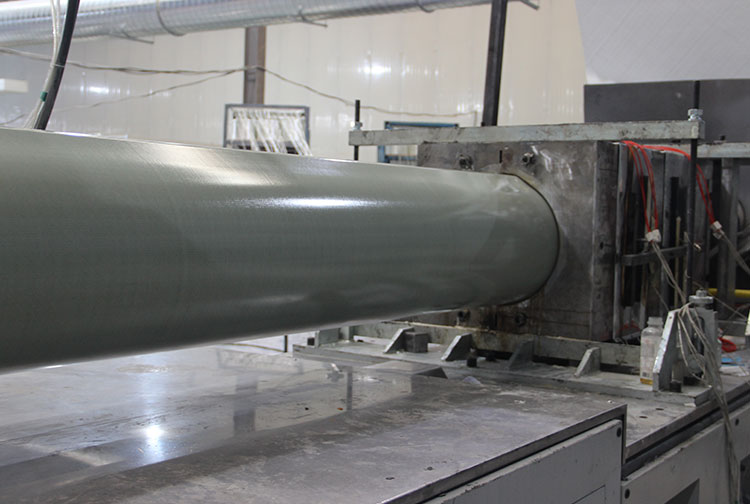
Pultrusion Process with Fiber Mat
Benefits of Using Fiber Mat in FRP Profiles
- Enhanced Mechanical Strength: Fiber mats distribute loads across the profile, increasing tensile and impact strength.
- Improved Resin Compatibility: Proper mat selection ensures better bonding with the resin, reducing voids and delamination.
- Dimensional Stability: Fiber mats maintain profile shape during curing and after exposure to environmental stresses.
- Cost Efficiency: Mats offer a balance between performance and material cost, making them ideal for high-volume production.
Performance Comparison: With vs. Without Fiber Mat
Property | Without Fiber Mat | With Fiber Mat |
---|---|---|
Tensile Strength | Low | High |
Flexural Strength | Moderate | High |
Impact Resistance | Poor | Good |
Shape Retention | Unstable | Stable |
Application Examples of Fiber Mat in FRP Profiles
FRP profiles reinforced with fiber mats are widely used in:
- Bridge decks and pedestrian walkways
- Cable trays and support systems
- Ladders and guard rails
- Structural beams and columns
- Window and door frames
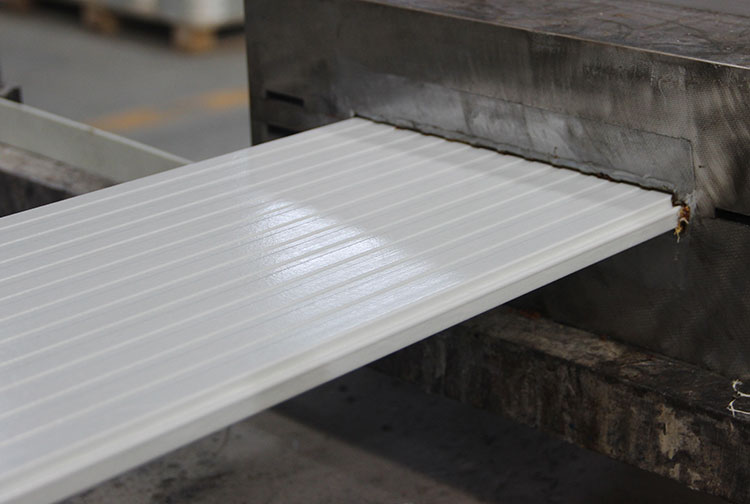
FRP Deck with Fiber Mat
How to Choose the Right Fiber Mat
When selecting a fiber mat for your FRP project, consider the following factors:
- Type of Load: Static vs. dynamic loading affects mat choice
- Resin Compatibility: Ensure the binder in the mat is compatible with your resin
- Application Environment: Moisture, temperature, and UV exposure requirements
- Production Process: Match mat form (roll, sheet, preform) with your production setup
Conclusion
Fiber mats are essential to the performance of FRP profiles. They provide strength, structural integrity, and durability in a cost-effective and efficient manner. Understanding their types, roles, and selection criteria can lead to better product quality and longer service life. Whether you're designing a bridge support or manufacturing window frames, investing in the right fiber mat can elevate the performance of your FRP solution.
Contact us today to learn more about our customized FRP profiles and high-quality fiber mat solutions tailored to your needs.