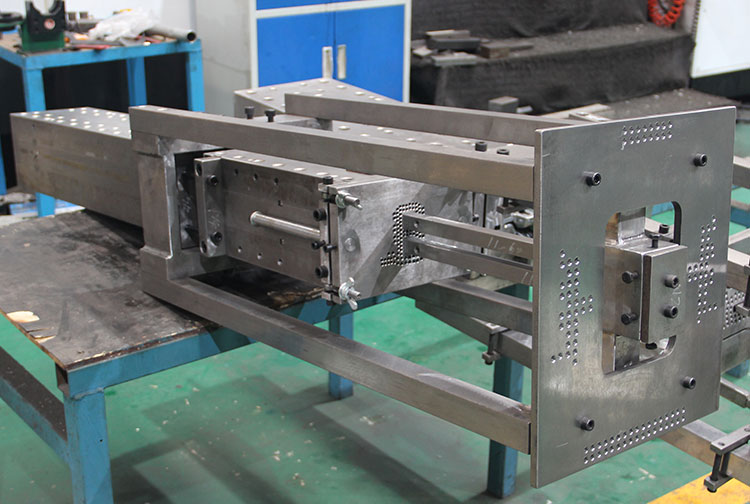
Composite Pultrusion Mold
The production of fiberglass reinforced plastic (FRP) profiles through the pultrusion process relies on advanced molds, known as pultrusion dies or pultrusion molds. These molds are essential for shaping continuous composite pultrusion profiles used in construction, aerospace, and other industries. This news article delves into the role of FRP pultrusion dies, focusing on their design, manufacturing, and maintenance.
Understanding Pultrusion Dies
A
pultrusion die is a precision tool that shapes fiber-reinforced composites during the pultrusion process. Unlike traditional molding, pultrusion pulls glass fibers and
thermoset resins through a
heated die to form profiles with consistent cross-sections. The
mold cavity within the
profile die determines the shape of the final product, such as rods or beams. The
continuous forming die ensures a seamless production process, making pultrusion ideal for high-volume manufacturing.
Materials and Manufacturing
Most
pultrusion molds are crafted from durable
steel dies to withstand the abrasive nature of glass fibers and high curing temperatures. The
die manufacturing process uses precision machining to create a smooth
mold cavity, ensuring consistent resin flow. Some systems incorporate a
resin injection mold to evenly distribute
thermoset resins, enhancing the structural integrity of the
composite pultrusion mold output. Advanced coatings are often applied to
precision dies to reduce wear.
Optimizing Die Design
Effective
die design is crucial for producing high-quality FRP profiles. The
mold cavity must be engineered to account for resin shrinkage and fiber alignment. The
heated die maintains precise temperature control to ensure proper curing, while complex
thermoset molds may feature multiple heating zones. A well-designed
profile die guarantees dimensional accuracy and a smooth surface finish.
Maintenance for Longevity
Die maintenance is vital to sustain production quality. The abrasive action of fibers can wear down the
mold cavity, affecting precision. Regular cleaning and inspection of the
steel die prevent defects, while maintenance of the
resin injection mold ensures consistent resin flow. A robust
die maintenance schedule minimizes downtime and extends the lifespan of the
continuous forming die.
Conclusion
The
pultrusion die is at the heart of
FRP pultrusion production, enabling the creation of strong, lightweight profiles. Innovations in
die design,
die manufacturing, and
precision dies continue to drive efficiency and quality. By prioritizing
die maintenance, manufacturers can ensure reliable performance of
composite pultrusion molds, meeting the growing demand for FRP profiles across industries.