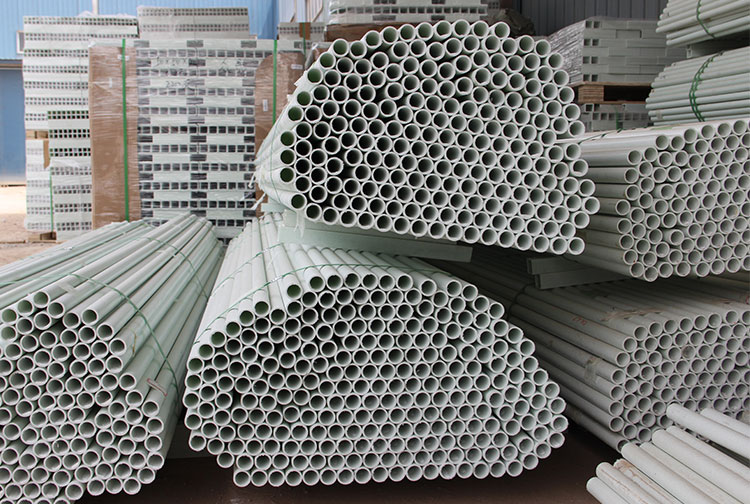
Customized FRP Profiles
Fiber Reinforced Plastic (FRP) profiles are widely used across industries due to their lightweight, high strength, corrosion resistance, and design flexibility. When purchasing customized FRP profiles, customers must pay close attention to specific factors to ensure the product meets their application requirements. This article explores three critical aspects: the classification and performance advantages of fiber felt, the classification and performance advantages of resin, and the use of additives to enhance FRP profile performance for specific applications.
1. Classification and Performance Advantages of Fiber Felt
Fiber felt serves as the reinforcement material in FRP profiles, providing structural strength and durability. The choice of fiber felt significantly impacts the mechanical properties and performance of the final product. Fiber felts are classified into several types, each with distinct characteristics:
- Glass Fiber Felt: The most common type, glass fiber felt is cost-effective and offers excellent tensile strength, impact resistance, and corrosion resistance. It is ideal for applications in construction, marine, and chemical industries.
- Carbon Fiber Felt: Known for its superior strength-to-weight ratio and stiffness, carbon fiber felt is used in high-performance applications such as aerospace and automotive components. However, it is more expensive than glass fiber.
- Aramid Fiber Felt: Aramid fibers, such as Kevlar, provide exceptional impact resistance and flexibility. They are often used in applications requiring high toughness, like protective gear and structural reinforcements.
- Hybrid Felt: Combines multiple fiber types (e.g., glass and carbon) to balance cost and performance, tailored to specific needs.
Performance Advantages:
- High Strength and Rigidity: Fiber felts enhance the load-bearing capacity of FRP profiles.
- Corrosion Resistance: Especially with glass and aramid fibers, felts ensure durability in harsh environments.
- Design Flexibility: Felts can be layered or oriented to achieve desired mechanical properties.
When selecting fiber felt, customers should consider the application environment, load requirements, and budget. For instance, glass fiber felt may suffice for general-purpose profiles, while carbon fiber is better suited for high-stress applications.
2. Classification and Performance Advantages of Resin
Resin acts as the matrix in FRP profiles, binding the fiber felt and transferring loads while protecting the fibers from environmental damage. The choice of resin directly affects the profile’s chemical resistance, thermal stability, and overall durability. Resins are classified into several types:
- Polyester Resin: Widely used due to its low cost and good mechanical properties, polyester resin is suitable for general-purpose FRP profiles in construction and industrial applications. It offers moderate chemical and thermal resistance.
- Vinyl Ester Resin: With improved chemical resistance and toughness compared to polyester, vinyl ester resin is ideal for corrosive environments, such as chemical plants or wastewater treatment facilities.
- Epoxy Resin: Known for its excellent adhesion, high strength, and thermal stability, epoxy resin is used in demanding applications like aerospace and high-performance structural components. It is more expensive but offers superior performance.
- Phenolic Resin: Offers excellent fire resistance and low smoke emission, making it suitable for applications requiring stringent fire safety standards, such as transportation and building interiors.
Performance Advantages:
- Environmental Protection: Resins shield fibers from moisture, chemicals, and UV exposure, extending the lifespan of FRP profiles.
- Thermal and Chemical Stability: Certain resins, like epoxy and vinyl ester, perform well in extreme conditions.
- Ease of Processing: Resins can be formulated for specific curing times and viscosities, enabling complex profile designs.
Customers should evaluate the operating environment and performance requirements when choosing a resin. For example, vinyl ester resin is preferable for profiles exposed to corrosive chemicals, while phenolic resin is better for fire-prone areas.
3. Adding Appropriate Additives to Enhance FRP Profile Performance
Additives are incorporated into FRP profiles to enhance specific properties based on the application scenario. These additives can improve fire resistance, UV stability, color, or mechanical performance, making them critical for customized profiles. Common additives include:
- Flame Retardants: Essential for applications in transportation, construction, or public infrastructure, flame retardants reduce flammability and smoke generation. For example, halogen-based or phosphorus-based additives can enhance fire resistance.
- UV Stabilizers: For outdoor applications, UV stabilizers protect FRP profiles from degradation caused by prolonged sunlight exposure, maintaining color and mechanical properties.
- Fillers: Materials like calcium carbonate or silica can reduce costs, improve dimensional stability, or enhance surface finish. However, excessive fillers may compromise strength.
- Pigments: Used to achieve desired colors or aesthetic effects, pigments are common in architectural or decorative FRP profiles.
- Impact Modifiers: These additives improve toughness and resistance to cracking, crucial for profiles subjected to dynamic loads.
Performance Advantages:
- Tailored Functionality: Additives allow FRP profiles to meet specific regulatory or environmental requirements, such as fire safety standards.
- Extended Service Life: UV stabilizers and corrosion-resistant additives enhance durability in challenging conditions.
- Cost Optimization: Fillers can lower production costs without significantly affecting performance.
When specifying additives, customers should clearly define the application scenario. For instance, profiles used in coastal areas may require UV stabilizers and corrosion-resistant additives, while those in public buildings may need flame retardants to comply with safety regulations.
Conclusion
Purchasing customized FRP profiles requires careful consideration of the materials and additives used in their production. By understanding the classification and performance advantages of fiber felt and resin, customers can select materials that align with their strength, durability, and environmental requirements. Additionally, incorporating appropriate additives ensures the profiles are optimized for specific applications, enhancing performance and longevity. By focusing on these three key factors—fiber felt, resin, and additives—customers can make informed decisions and achieve high-quality, tailored FRP solutions for their projects.