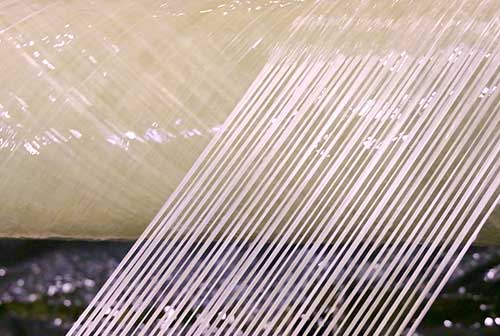
Filament winding and pultrusion are two of the most common methods for manufacturing composites. Both methods involve the use of continuous fibers and a resin matrix to create a strong, lightweight material. However, there are some key differences between the two methods that make them suitable for different applications.
Filament winding
Filament winding is a process in which continuous fibers are wound onto a mandrel in a predetermined pattern. The fibers are then cured to form a solid, composite part. Filament winding is a versatile process that can be used to produce a wide variety of shapes and sizes. It is often used to manufacture pipes, tubes, and other cylindrical parts.
Advantages of filament winding
High strength and stiffness: Filament-wound composites are typically very strong and stiff, making them ideal for applications where high mechanical performance is required.
Good dimensional accuracy: Filament winding can be used to produce parts with high dimensional accuracy, making it a good choice for applications where close tolerances are important.
Wide range of shapes and sizes: Filament winding can be used to produce a wide variety of shapes and sizes, making it a versatile process for a variety of applications.
Disadvantages of filament winding
High cost: Filament winding can be a relatively expensive process, especially for large or complex parts.
Limited automation: Filament winding is a labor-intensive process that is not easily automated.
Pultrusion
Pultrusion is a process in which continuous fibers are pulled through a resin bath and then through a heated die. The fibers and resin are then cured to form a solid, composite part. Pultrusion is a continuous process that can be used to produce long, straight parts with a uniform cross-section.
Advantages of pultrusion
High production rate: Pultrusion is a continuous process that can produce parts at a high rate, making it a cost-effective option for mass production.
Good dimensional stability: Pultruded parts are typically very dimensionally stable, making them a good choice for applications where close tolerances are important.
Wide range of applications: Pultruded composites are used in a wide range of applications, including aerospace, marine, and construction.
Disadvantages of pultrusion
Limited shape complexity: Pultruded parts are typically limited to straight or slightly curved shapes.
Reduced strength and stiffness: Pultruded composites are typically not as strong or stiff as filament-wound composites.
Comparison- Strength and stiffness
Filament-wound composites are typically stronger and stiffer than pultruded composites. This is because the fibers in filament-wound composites are aligned in the direction of the applied load, while the fibers in pultruded composites are oriented in a variety of directions.
Dimensional accuracy
Filament winding and pultrusion can both be used to produce parts with high dimensional accuracy. However, filament winding is typically more accurate than pultrusion for complex shapes.
Shape complexity
Pultrusion is limited to straight or slightly curved shapes, while filament winding can be used to produce a wider range of shapes.
Production rate
Pultrusion is a continuous process that can produce parts at a high rate, while filament winding is a batch process that is more labor-intensive.
Cost
Pultrusion is typically a more cost-effective process than filament winding, especially for large or complex parts.
Applications
Filament winding is often used to manufacture pipes, tubes, and other cylindrical parts. It is also used to produce structural components, such as beams and columns. Pultrusion is used to manufacture a wide range of parts, including rods, tubes, beams, and panels. It is also used in the aerospace, marine, and construction industries.
Conclusion
Filament winding and pultrusion are both valuable manufacturing methods for composites. The best method for a particular application will depend on the specific requirements of that application.
Additional considerations
In addition to the factors discussed above, there are a few other considerations that should be taken into account when choosing between filament winding and pultrusion. These include:
The available equipment: Filament winding requires specialized equipment that may not be available to all manufacturers, while pultrusion can be done with relatively simple equipment.
The required quality: Filament winding can be a more labor-intensive process than pultrusion, which can lead to higher